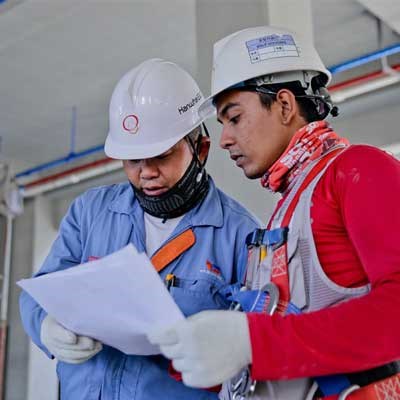
During construction, workers must be urged to make safety designs for these corners and corners, and all waterproof coatings must be applied in place.
1. Design and construction of waterproof layer in kitchen and bathroom
There are waterproof layers under the floors of our bathrooms and kitchens. In the traditional practice, a waterproof layer of two felts and three oils or three felts and four oils is often used. Now this kind of thermal processing has been basically eliminated.
1.1. Choose waterproof coating
At present, most construction units use waterproof coatings. Although this is simpler than the construction procedure of two felts and three oils. However, there is a strong peculiar smell during construction, and a slightly larger floor pipe joint will cause hidden dangers. The best solution is to mix the cement mortar with a waterproofing agent, which is simple and reliable, and will never cause cracks and aging. The joints should be painted in place. The joints between the bathroom walls and the ground and the joints between the water pipes and the ground are the most prone to problems. The waterproof layer of the bathroom is extremely easy to be damaged during decoration, especially the joints between the downpipe and the floor slab are the most likely to leak, which will cause trouble to the residents on the lower floors. Therefore, during the decoration process, this part of the project must be strictly checked.
1.2. Don't damage the waterproof layer
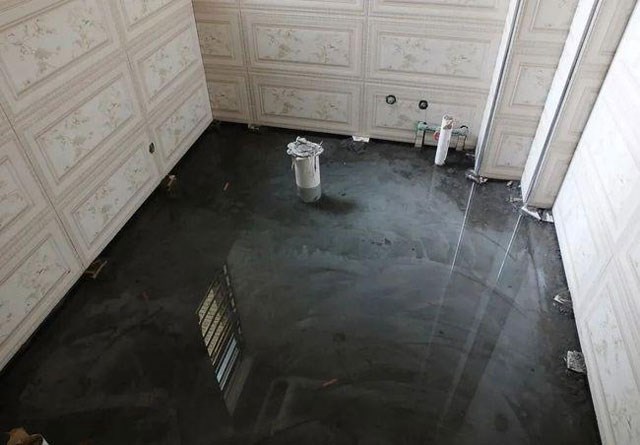
What needs to be reminded is that if the owner accidentally damages the waterproof layer during the decoration process and needs to be rebuilt, he must pay attention to the "24-hour water storage experiment" after rebuilding. The specific method is to block all the water in the bathroom after completion of the bathroom construction, and build a 25 cm high "ridge" at the door, and then pour 20 cm high water into the bathroom. After 24 hours of water storage, check the surrounding walls and ground for leakage. This 24-hour flood inspection is the key to ensuring the quality of the bathroom waterproofing project. Although it is troublesome, it must be done.
2. Design and construction of glass walls
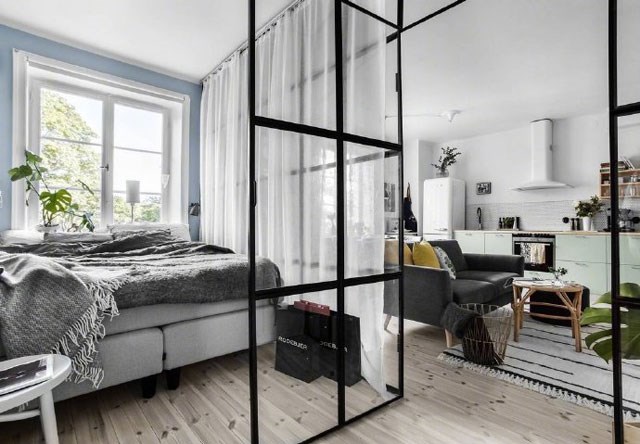
The design and construction of the glass wall are mainly viewed from the following aspects:
2.1. How to hide
The upper and lower, left and right two corresponding sides (four perimeters) are completely glued to the aluminum alloy frame by structural glue. If only one of the two corresponding sides of the glass is hidden, and one corresponding side can be seen, it is the semi-hidden frame glass curtain wall. The three advantages of this kind of curtain wall are beautiful, energy-saving and easy to maintain.
2.2. Light pollution
When the sun shines strongly, the light reflected by the glass curtain wall is bright and dazzling. If people work and live in this white light pollution environment for a long time, the retina and iris will be damaged to varying degrees, the vision will drop sharply, and the incidence of cataracts will be as high as 45%. It also makes people dizzy and upset, and even suffers from insomnia, loss of appetite, depression and other symptoms similar to neurasthenia. In summer, the strong reflected light from the glass curtain wall enters the nearby residential buildings, which also increases the indoor temperature and affects normal life. Some glass curtain walls are semi-circular, and the reflection of light can easily cause fire.
2.3. Types of glass curtain walls
Glass curtain wall construction may bring light pollution and other hazards, but it does not mean that glass curtain walls should not be made, but the focus is on how to make glass curtain walls. Many glass curtain walls that produce light pollution are caused by unscientific design and construction. Therefore, this problem can be solved by a proper structure.
2.3.1. Double glazing
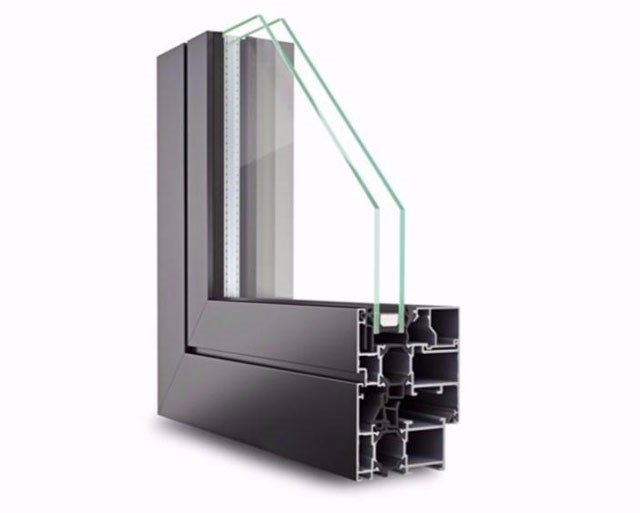
This structure has different functions in different seasons. In summer, put down the translucent roller blinds, open the exhaust ducts and vents, and remove most of the radiant heat after being reflected by the curtains: in winter, close the vents and turn off the exhaust fan. The double-glazed glass can play a role in heat preservation. To prevent indoor heat loss, the disadvantage of this structure is that the investment cost is relatively large.
2.3.2. Infrared heat-absorbing glass
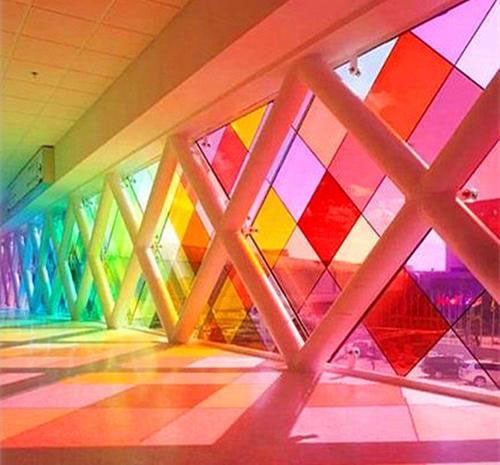
This structure uses the infrared transmission characteristics of the dielectric film coating, and the hot water pipe can be used to heat water through the heat energy in the sun, and it can be used effectively in both summer and winter.
3. Design and construction of TV background wall
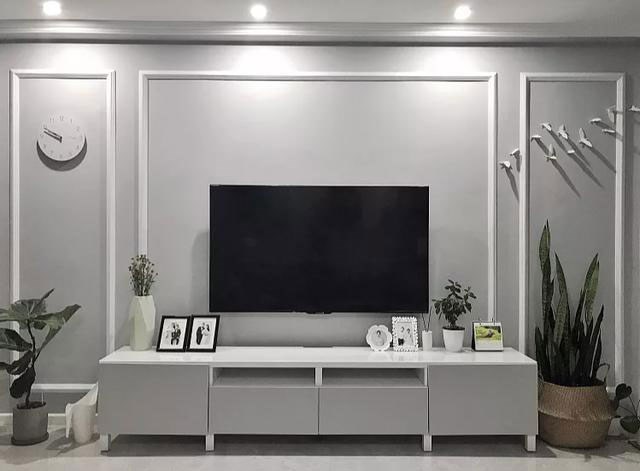
When designing the wall, leave a place for the embedded pendants, a solid base and enough power sockets.
3.1. Installation of wall-mounted TV
Experts suggest that it is better to bury a thicker PVC pipe in the dark, all the wires can reach the TV below through this pipe: power supply part-must ensure reliable grounding, after the circuit transformation, it needs to pass professional tests For the instrument, check whether the contacts of the socket are reliable, and whether there is a reverse connection of the neutral and ground wires. If possible, check whether the cable TV radio frequency cable is truly grounded. Because if the RF cable is not completely grounded, it will form a certain potential difference (ie voltage) with the power supply. For the LCD TV in the standby state, it is very easy to cause the internal wiring of the fuselage to overheat, thereby causing a fire hazard.
3.2. The TV background wall should generally correspond to the partial ceiling on the top surface
Lighting lamps are generally installed on the suspended ceiling. Because when you turn off the light when watching TV, the room becomes pitch black, but the electric display screen is very bright, one black to bright, and the contrast of light is very strong. After watching for a long time, the eyes will be very tired, easy to cause soreness, discomfort, and even headaches. . If you turn on some background lights appropriately, the TV image will feel softer and clearer, and your eyes will be comfortable. Therefore, it is necessary to consider the matching of the wall shape and the lighting, as well as the color and intensity of the lighting. It is best not to illuminate the TV with strong light to avoid eye fatigue.
3.3. The size of the TV wall should be appropriate
Don't make the TV wall too thick or too big, it will make the living room small and narrow, and it will also affect the visual effect of the TV. In addition, it is best to determine the position of the TV after the position of the sofa is determined. Generally speaking, the best distance between the eyes and the TV should be 3.5 times the size of the TV. The center of the TV screen should be in line with your eyes, too high or too low will affect the comfort of viewing.
3.4. Color selection should be appropriate
Many young people like to use some colorful and exaggerated background wall styles. Although it looks good at the beginning, it will cause a certain visual fatigue in the long run. Therefore, we still recommend the design of the TV background wall. Those soft and concise styles.
4. Design and construction of walls and floors
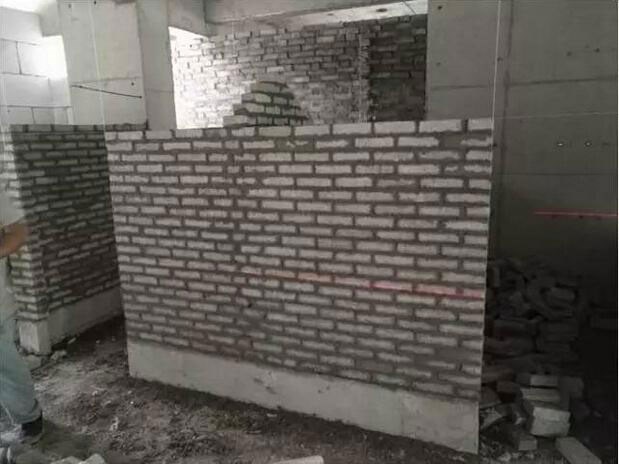
Wall and floor slab design often takes structural safety and durability into consideration, which requires the owner to take it seriously.
4.1. Method of wall inspection
It is necessary to observe whether there are cracks on the outer wall of the house to prevent the hidden danger of water leakage. Secondly, look at whether there are cracks in the load-bearing wall, whether the crack runs through the entire wall and goes to the back, whether there is an inclined crack, if it does, it means that the house has a structural safety hazard. Finally, look at whether there are through cracks in the load-bearing wall and there are directional and regular cracks in the same position on the walls of different floors. This kind of structural safety hazard should be paid more attention to and should be reported to the relevant departments in time.
5. Ways to prevent cracks
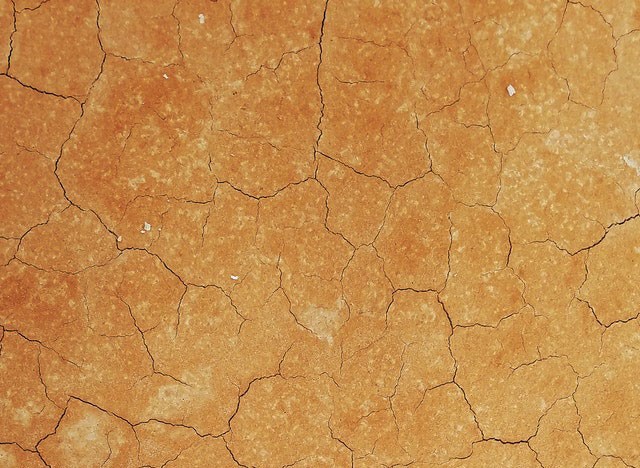
Due to the susceptibility to air humidity and the difference in deformation with the frame structure, the tie bars on both sides of the wall should be pulled through to improve the crack resistance. After the masonry is completed, it is necessary to insist on sprinkling and curing to reduce the drying shrinkage of the mortar.
5.1. Start with decoration materials
Among the quality performance indicators of lightweight blocks, the shrinkage has the greatest impact on the generation of wall cracks, and the relative moisture content is an important indicator of shrinkage. For this reason, it is required that light-weight blocks, especially small light-aggregate concrete blocks, must be cured for 28 days before they can leave the factory, and the user must insist on product acceptance to prevent the use of unqualified products. After the blocks enter the site, waterproof measures should be taken in advance to ensure that the main structure is maintained with water and rainwater does not flow into the floor. In order to increase the age of the blocks as much as possible, it is advisable to carry out masonry after an interval of one week, and the water content of the blocks should be measured by the electrothermal method. When the moisture content is lower than 50%, construction is allowed. Before masonry, water should not be watered and moistened in advance, but an appropriate amount of water should be applied to the masonry surface before laying the mortar.
5.2. Start with design and construction
To prevent cracks in lightweight block walls, architectural design must be the focus. According to the relevant regulations and requirements of the decoration, combined with the function of the building and the characteristics of the material, effective structural measures can be taken to avoid wall cracking and leakage. Generally, when the wall length exceeds 4 meters, a structural column should be installed, and when the wall height exceeds 3 meters, a ring beam should be installed. When the wall length and storey height is large and there is a door opening, the construction of the column should first ensure both sides of the opening to avoid shrinkage and cracks at the corners of the opening. When the main structure does not have steel bars, or the position is deviated, planting bars must be used.